전자제품 세척 가이드
전자 장치용 인쇄 회로 기판(PCB) 조립, 재작업 또는 수리 과정에서 PCB 세척 여부에 대해 알아야 합니다. 세척하려면 시간과 경비가 들어가며, 잘못하면 더 안좋아질 수 있습니다. 이 가이드에서 PCB를 세척하는 이유와 전자장치 세척에 대한 모범 관례에 대해 다루겠습니다.
주제 색인
- 인쇄 회로 기판(PCB)을 세척하는 이유
- 이온 오염이란?
- 노출된 기판 제작으로 인한 가장 일반적인 이온 오염
- 전자 회로 기판의 흰 잔여물이란?
- 이온 오염 시험 방법
- 전자 회로 기판의 흰 잔여물 제거 방법
- 전자 회로 기판 세척 방법
- 플럭스 타입이 PCB 세척 과정의 효과성에 영향을 끼치나요?
- PCB에서 플럭스 잔여물 제거를 어렵게 하는 요인
- 납땜 후 PCB를 세척하는 방법
- 세척 효과를 높이기 위해 에어로졸 플럭스 제거제에 스트로 부착장치를 사용하는 방법
- 에어로졸 플럭스 제거제로 구성품 아래를 세척하는 방법
- 에어로졸 플럭스 제거제를 사용할 때 세척 효과에 영향을 주는 분사 각도
- 브러시, 스왑, 와이프와 같은 세척 공구를 올바르게 사용하는 방법
- When Is a Final Rinse Required When Cleaning a PCB 세척에 마무리 린스가 필요한 시점
- 가장 인기 있는 전자장치 세척제
인쇄 회로 기판 (PCB)를 세척하는 이유
PCB 세척이 항상 필요하지 않으며 생산 또는 수리에 시간과 경비가 추가되므로 세척이 타당한지 입증할 필요가 있습니다.
PCB 외관 개선
PCB 계약 제조자라면 기판 외관은 이미지에 반영되는데요. 기름기와 같은 잔여물이 납땜 이음부 주변에 없으면 고객의 QC 검사관이 깃발을 올릴 수 있습니다. 플럭스 잔여물이 납땜 이음부를 까맣게 만들고 얼룩이 졌다면 결함으로 보일 수 있습니다. 재작업으로 생긴 플럭스 잔여물이라면 문제가 아니더라도 주의를 환기시키기 위한 결함 태그 역할을 합니다.
PCB 신뢰성 개선
신뢰성 요구사항은 일반적으로 최종 제품 특성에 따릅니다. 컴퓨터 키보드와 같은 사용후 버리게 되는 제품의 경우 작동이 멈추어도 생명을 잃지 않습니다. 이 경우 EMS 공급자는 no-clean 플럭스를 사용하고 세척 과정은 포기할 수 있습니다. 반면에, 기판 고장이 사망을 직접 초래할 수 있는 심장 박동기 전자장치의 요구사항은 훨씬 더 엄격 하게 됩니다. 이 예로 조립과 그 다음의 재작업 이후 세척이 필요해지며, 효과성과 반복성에 대해 이 과정이 엄격히 검증됩니다. 수명이 긴 제품은 강성 시험과 제어장치 없이 세척 요건 범위에 들어갈 수 있습니다.
PCB와 구성품 부식 예방
전자 회로 기판의 플럭스 잔여물은 산성입니다. 세척 과정으로 제거하지 않으면 주위 공기로부터 수분을 흡수하여 구성품 납과 PCB 접촉장치에 부식을 일으킬 수 있습니다.
Corrosion on failed assembly in QFP area (photo courtesy of Foresite)
컨포멀 코팅을 이용한 접착 문제 방지
대부분의 사람들은 페인트 칠을 할 때 표면을 처리해야 하므로 완전히 깨끗이 해야 한다는 것을 알고 있습니다. 그렇지 않으면 페인트가 표면에서 빨리 떨어지고 벗겨집니다. 마찬가지로, no-clean 플럭스로 인한 오염인 경우에도 컨포멀 코팅도 그렇습니다. “No-clean”은 납땜 후 남은 이온 물질의 양을 가리킵니다. 코팅이 붙어 있는 여부와 관계가 없습니다.
코팅을 하기 전에 PCB에 플럭스 잔여물이 남아 있을 때 기판 표면에서 코팅이 들리거나 얇은 조각으로 갈라지는게 일반적입니다. 포켓이 전체 표면이 아닌 납땜 이음부 주변에서 분리되어 있는 경우에 확실히 그렇습니다 (PCB 웨이브 납땜 하부 예외).
설상가상으로 일반적으로 코팅은 반투수성이어서 어느 정도는 통기성이 있습니다. 수분이 플럭스 잔여물에 들어가고 적실 수 있으며, 부식을 발생시킬 수 있습니다.
코팅을 들리게 하는 플럭스 잔여물 (photo courtesy of NPL)
이온 오염으로 인한 수상돌기 증가 방지
극성 또는 플럭스 잔여물 또는 기타 원인으로 인해 남은 이온 입자는 주위 공기의 수분에 노출되거나 전류가 가해질 때 수상돌기라고 하는 가지 또는 사슬로 연결될 수 있습니다 (그림 1). 이 수상돌기는 전도성으로 트레이스를 형성하여 전류 누설을 일으키거나 시간이 더 길어지면 단락도 일으킬 수 있습니다.
Fig 1 – 수상돌기 형성
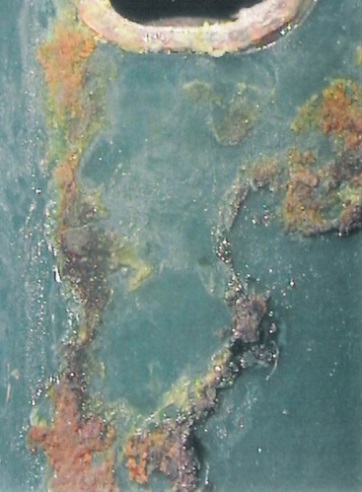
이온 오염으로 인한 납 패드 사이의 수상돌기 증가 (photos courtesy of Foresite)
이온 오염이란?
극성 오염이란?
이온 오염은 조립 과정에서 남은 플럭스 잔여물입니다. 이온 화합물은 정전력에 의해 결합되어 있으며, 영의 순 전하를 갖습니다. 이 물질은 물에 노출되면 분리되는데 양전화를 띠는 양이온과 음전하를 띠는 음이온으로 이루어졌습니다. 간단한 예를 들자면 하나의 양이온의 나트륨으로 이루어진 식염 (염화나트륨)은 1개의 전자가 결핍되고, 음이온을 띠는 염화물(CI)는 전자가 더 있습니다. 반면에, 극성 화합물은 분자 한 측에 양전하가 있고, 다른 분자 측에 음전하가 있을 수 있으며, 이 분자들은 절대로 분할되지 않습니다. 물, 아이소프로판올 (또는 IPA)는 극성 분자의 한 예입니다.
기판에 구성품이 많으면 구성품 또한 절삭유, 살생물제, 부식 방지제 등 다양한 이온/전도성 오염물질을 어셈블리에 옮길 수 있습니다. 또한 조립 단계 (공정오일, 이형제(mold releases) 등)에 영향을 줄 수 있는 비이온 물질을 조심해야 합니다.
노출된 기판 제작으로 인한 가장 일반적인 이온 오염
“레이어링” 과정에서 포집되는 일반 수분
물은 극성 오염물로 전도성 사고의 원인이 되는 다른 이온 물질을 분리하는 전도성입니다 (수송돌기 증가, ECM 등). 외부 수분을 제거하기 위해 기판을 “베이킹”하는 것이 일반적입니다.
PCB 제작 관련 오염으로 인한 부식 (전면 사진)
에칭 화학물질
이 물질은 전도성이 매우 높을 뿐만 아니라 부식성입니다. 화학적으로 중화되고 제거되며, 전류 누설의 원인으로 알려져 있습니다.
납땜으로 인한 플럭스 잔여물
구리 부식이 눈에 띄는 걸쭉한 no-clean 플럭스 잔여물 (전면 사진)
플럭스 잔여물은 잘 알려져 있는데요. 액체, 코어드 와이어(cored wire) 또는 페이스트 형태인 플럭스는 제거하지 않으면 심각한 신뢰성 결함을 일으킬 수 있습니다. 납땜 과정에서 생기는 일반 전도성 플럭스 잔여물로는 다양한 비반응 활성제, 결합제, 유동성 조절제, 감화제(saponifier)가 있을 수 있습니다. 이 물질들은 산성 (아비에트산(abietic), 아디프산(adipic), 숙신산(succinic)) 물질이 많으며, 아미노 화합물이 주성분이고, 심지어 “비누”에서 발견되는 인산 및 황산 이온과 같은 성분이 있습니다. 증기 탈지 작용을 하는 강한 세척제 또는 제조 환경에서 볼 수 있는 일반 배치 또는 인라인 세척제의 수성 화학제로 기판에서 전부 제거해야 합니다.
드릴링 및 도금 공정에서 생긴 층간 잔여물
이온 오염으로 인한 땜납 패드 사이에 증가한 수상돌기 (전면 사진)
이러한 잔여물 외에도 세척 과정에서 생긴 잔여물도 제거해야 합니다. 이 잔여물은 수성 세척 시스템에서 더 자주 눈에 띱니다. 대부분 플럭스 잔여물을 중화하고 유화하기 위해 감화제를 사용합니다. 이 성분들은 극성이 높은 이온 성분으로 제거하지 않으면 수상돌기 및/또는 ECM 메커니즘을 높일 수도 있습니다. 또한, 이러한 제품에 부식 방지제와 계면 활성제가 일반적으로 쓰입니다. 이 자체는 나쁘지 않지만 세척 과정에서 오염물과 함께 주의해서 제거해야 합니다.
이온 오염 시험 방법
저품질의 PCB 제작에서부터 납땜, 집중된 구성품, 최종 세척 단계에 이르기까지 전부 오염의 원인이 될 수 있습니다. 이 중에 대부분은 ROSE 시험, 이온 추출, 크로마토그래피와 같은 이온 오염 시험 및 분석, 프로젝트 초기에 실시하는 높은 습도 시험 중에 발견될 수 있습니다.
PCB 조립 시 엄격한 품질 관리 및 표준 운영 절차와 어셈블리 제조 및 검증 시험 단계는 신뢰성이란 문제를 방지하는데 오래 걸릴 수 있습니다. 장갑을 끼지 않고 작업자가 부품을 잘못 취급하면 피부의 염분과 오일이 기판으로 들어가서 손상을 일으킬 수 있다고 생각해보십시오.
전자 회로 기판의 흰 잔여물이란?
흰 잔여물은 일반적으로 비효율적인 PCB 세척과 관련한 증상입니다. 납땜 과정에서 생기는 일반적인 전도성 플럭스 잔여물로는 다양한 비반응 활성제, 결합제, 유동성 조절제, 감화제(saponifier)가 있을 수 있습니다. 이 물질들은 산성 (아비에트산(abietic), 아디프산(adipic), 숙신산(succinic)) 물질이 많으며, 아미노 화합물이 주성분이고, 심지어 “비누”에서 발견되는 인산 및 황산 이온과 같은 성분이 있습니다. 세척제로 모든 성분이 완전히 용해되지 않거나 PCB에서 세척제가 흘러내리지 않아야 한다면, 잔여 용제가 증발하고 물 얼룩과 같거나 흰색의 잔여물이 남을 수 있습니다.
구리 부식이 눈에 띄는 흰 플럭스 잔여물 (전면 사진)
전자 회로 기판에서 흰 잔여물 제거 방법
흰 잔여물은 플럭스 제거제로 보통 제거할 수 있습니다. 잔여물이 초기 세척 과정에서 불충분하게 용해되지 않은 것이라면 더 강한 세척제가 필요할 수 있습니다. 와이프, 스왑, 브러시 또는 브러시 부착장치가 있는 에어로졸을 포함할 수 있는 섞는 작업이 필요합니다. 다음의 단계에 따라 흰 잔여물을 제거합니다.
- 강한 용제를 잔여물에 분사합니다.
- 해당 부위가 젖어 있을 때 와이프, 스왑 또는 브러시와 같은 세척 공구로 문지릅니다.
- 세척한 부위와 주변 영역에 동일한 용제를 분사하고 기판을 기울여 린스가 흐르게 합니다.
브러시 부착장치가 있는 Flux-Off Rosin
전자 회로 기판 세척 방법
PCB 플럭스 제거 작업은 일반적으로 수동 세척 방식이 필요한 작업대에서 이루어질 수 있습니다.소량의 전자 PCB 조립, 재작업 및 수리에 일반적인 작업입니다. 수동 세척 방법은 일반적으로 더 손이 가고 덜 반복적이므로 작업자마다 결과가 다를 수 있습니다. 대량 조립 또는 가변성이 더 적은 경우 더 자동화된 세척 방법을 사용합니다.
수동 플럭스 제거 방법
- Aerosol- 에어로졸 플럭스 제거제는 밀폐 시스템으로 항상 깨끗한 용제가 분사되고 분사 압력 및 패턴에 의해 섞입니다. 스트로 부착장치는 보통 더 정밀하게 분사하는데 사용됩니다.
- 에어로졸 w/브러시 부착장치- 용제가 문지를 때마다 브러시를 통해 분사되도록 에어로졸 노즐에 브러시가 추가될 수 있습니다.
- 트리거 스프레이- 트리거 스프레이는 수성 세척제와 이소프로필 알코올(IPA)에 더 일반적이지만 강력한 솔벤트 세척제용은 아닙니다.
- 액체 담금- PCB를 솔벤트 세척제 트레이 또는 양동이에 담글 수 있으며, 잘 떨어지지 않는 오일에 필요한 스왑과 브러시와 같은 세척 공구를 사용할 수 있습니다. 용제를 가열하여 세척 효과를 높일 수 있지만 불연성 플럭스 제거제로만 해야 합니다.
- 스왑을 이용한 얼룩 세척- 코튼 또는 폼 스왑을 종종 펌프 디스펜서 또는 “도버”의 이소프로필 알코올과 같은 순한 용제로 적실 수 있습니다.
- 사전에 적시는 와이프와 스왑- 더 편리하게 사용하기 위해 이소프로필 알코올과 같은 순한 용제로 와이프와 스왑을 미리 적실 수 있습니다.
자동 또는 반자동 플럭스 제거 방법
- Ultrasonic- 초음파 세척 장비는 초음파로 플럭스 잔여물 내에 내파를 일으켜서 분해하고 PCB에서 들리게 만듭니다. 대부분의 장비는 세척 성능을 높이기 위해 용제를 가열하는 옵션이 있는데 불연성 플럭스 제거제에만 사용해야 합니다. 교차 오염이 문제가 될 수 있으므로 용제를 정기적으로 바꿉니다. 초음파 세척은 세라믹이 주성분인 레지스터와 같은 민감한 부품 및 소재에 너무 강할 수 있습니다.
- 증기 탈지제- 증기 탈지는 항공과 의료 전자제품과 같이 최고 정밀 세척에 적합한 방법입니다. PCB를 초음파로 채운 린스에 끓는 용제에 담그고, 용제 증기로 씻을 수 있습니다. 공비혼합물(azeotropes) 또는 비슷한 특수 용제가 필요합니다. 따라서 용제가 기화되면서 바뀌지 않고 연속 주기로 환원됩니다.
- 배치 플럭스 제거제- 기본적으로 전자 회로 기판용 디시와셔. 선반에 PCB이 고정되거나 플럭스 제거제 (일반적으로 수성)이 어셈블리에 분사됩니다. PCB는 기계가 세척, 헹굼 및 건조 주기를 거치는 동안 제자리를 유지합니다.
- 인라인 플럭스 제거제- 인라인 와셔는 전자 회로 기판용 카와시(car wash)와 더 비슷합니다. PCB는 컨베이어에 올려져서 세척, 헹굼 및 건조 영역을 통과합니다. 수성 플럭스 제거제를 사용합니다.
PCB 세척 효과에 영향을 주는 플럭스 타입
플럭스 타입은 세척에 큰 영향을 줄 수 있습니다. R, RA 및 RMA 플럭스는 일반적으로 일반 플럭스 제거제와 이소프로필 알코올로 제거가 더 쉽습니다. No-clean 플럭스는 PCB 상에 있기 때문에 제거가 더 어려울 수 있습니다. 더 강력한 솔벤트 플럭스 제거제, 브러시 또는 가열된 용제와 같은 추가 섞음이 필요할 수 있습니다. 수성 플럭스는 일반적으로 감화제가 섞인 물 또는 탈염수가 있는 배치 또는 인라인 세척 시스템으로 제거합니다. 알코올계 또는 특수 배합된 용제 또한 수성 플럭스에 사용할 수 있지만 동일한 세척제는 다른 타입의 플럭스에 여러 가지 결과를 보여줄 수 있습니다.
답은 플럭스 타입에 맞는 플럭스 제거제를 사용하는 것입니다. 이것은 다양한 고객이 요구하는 다양한 플럭스를 사용해야 하는 EMS 공급자에게 어려운 일이 될 수 있습니다. 플럭스 제거제는 다양한 플럭스로 나뉠 수 있으며 세척 시간, 섞음 및 열 추가와 같은 변수가 있을 수 있습니다.
배치 또는 인라인 세척 시스템의 수성 세척제의 경우 효과를 높이기 위해 세척제 농도를 조정할 수 있으며, 주기 시간을 늘리고 온도를 높일 수 있습니다.
PCB에서 플럭스 잔여물 세척을 어렵게 할 수 있는 요인
공정 엔지니어는 반복적인 과정 설계가 변수를 제어하는게 핵심이라고 말해줄 겁니다. 전자 회로 기판에서 플럭스를 제거할 때 세척제와 세척 과정의 성과를 급격하게 변화시킬 변수가 많습니다.
- 플럭스 타입 – 플럭스 타입은 세척 과정에 크게 영향을 끼칠 수 있습니다. R, RA 및 RMA 플럭스는 일반적으로 일반 플럭스 제거제와 이소프로필 알코올로 제거하기가 더 쉽습니다. No-clean 플럭스는 PCB 상에 있어서 제거하기가 더 어려울 수 있습니다. 더 강력한 솔벤트 플럭스 제거제 그리고 추가적으로 가열한 용제 또는 브러시와 같은 섞음이 필요할 수 있습니다. 수성 플럭스는 일반적으로 감화제가 섞인 물 또는 탈염수가 있는 배치 또는 인라인 세척 시스템으로 제거합니다. 알코올계 또는 특수 배합된 용제 또한 수성 플럭스에 사용할 수 있지만 동일한 세척제는 다른 타입의 플럭스에 여러 가지 결과를 보여줄 수 있습니다.
- 더 단단한 고체 플럭스 – 여러 납땜 기술을 혼합한 PCB 세척은 특히 어려울 수 있습니다. 잘 떨어지지 않는 플럭스 또는 더 단단한 고체 타입은 세척하기가 더 어렵고 더 긴 세척 시간, 담금 시간 또는 추가적인 섞음이 필요할 수 있습니다.
- 플럭스 양 – 플럭스 잔여물 층이 더 두꺼울수록 제거할 오염물이 더 많으며, 낮게 떨어져 있는 구성품 아래에 플럭스 댐을 형성할 수 있습니다. 이것은 플럭스 제거제가 구성품 아래에서 완전히 스며드는데 방해가 됩니다.
- 납땜 온도 – 온도가 높을수록 플럭스 잔여물을 가열할 가능성이 더 커져서 제거하기 더 어렵게 만듭니다. 고온 납땜은 더 긴 세척 시간, 담금 시간 또는 추가적인 섞음이 필요할 수 있습니다.
- 납 무함유 납땜 – 납 무합유 땜납은 일반적으로 더 높은 납땜 온도와 더 많이 활성화된 플럭스가 필요합니다. 납 무함유 납땜 과정에서 남은 플럭스 잔여물은 더 긴 세척 시간, 담금 시간 또는 추가적인 섞음이 필요할 수 있으며, 납 무함유 작업에 대해 설계된 더 강력한 플럭스 제거제를 고려해야 할 수 있습니다.
- 납땜과 세척 과정 사이의 시간 – 금요일에 조립을 끝마치고 월요일에 돌아오면 흰 플럭스 잔여물 때문에 놀라게 되는 일은 흔합니다. PCB 상에 고착된 플럭스 잔여물은 휘발 물질이 계속 플래싱 오프되면서 제거하기가 더 어려워집니다.
흰 잔여물 또는 전에 없었던 다른 세척 문제 때문에 갑자기 놀랬다면 도움을 요청하기 전에 작업 과정을 한 발짝 물러나서 살펴봅니다. 이것은 기술자가 처음에 하는 질문이 되며, 문제를 파악하고 해결하는데 필요합니다.
납땜 후 PCB 세척 방법
납땜 플럭스 제거 방법
수리 부위에서 플럭스 잔여물을 세척하는 가장 일반적인 방법은 이소프로필 알코올 또는 다른 세척제로 코튼 또는 폼 스왑을 적신 후 해당 부위를 문지릅니다. 이 작업이 플럭스에 충분할 수 있지만, RA 또는 수성과 같이 매우 활성화된 플럭스를 제거하는 경우 충분히 세척되지 않을 수 있습니다. 사실 플럭스 잔여물은 용제와 함께 증발하지 않습니다. 플럭스를 용해시키고 일부 잔여물이 스왑에 흡수되겠지만 대부분의 잔여물은 기판 표면에 다시 고착됩니다. 대부분의 경우 일반 플럭스보다 흰 잔여물이 제거하기가 더 어렵습니다.
플럭스 잔여물은 용제와 함께 증발되지 않습니다.
빠르고 쉽게 개선하는 방법 한 가지는 수리 부위를 스왑으로 흡수한 후 기판을 씻어내는 것입니다. 용제가 여전히 젖어 있는 동안 에어로졸 플럭스 세척제를 전체 기판에 분사합니다. 잔여물과 함께 용제가 기판에서 흘러내리는 각도로 PCB를 기울입니다.
에어로졸 플럭스 제거제와 함께 제공되는 스트로 부착장치는 구성품 아래에서 분사력을 높이는 좋은 도구입니다.
구성품 아래 세척에 좋은 스트로가 있는 에어로졸
켐트로닉스는 다양한 플럭스 제거제를 포함하는 BrushClean 시스템을 제공하고 있습니다. 세척제는 브러시를 통해 분사되어서 분사하는 동안 문지르는 동안 섞음 효과가 상승될 수 있습니다. 플럭스 잔여물을 흡수하기 위해 보푸라기가 없는 폴리셀룰로오스(poly-cellulose) 와이퍼를 수리 부위에 올려 놓고 분사하고 문지를 수 있습니다. 그 다음에 와이프와 브러시 부착장치를 제거하고, 기판 위에 분사하여 마지막으로 씻어냅니다.
와이퍼 위의 에어로졸 브러시 부착장치는 플럭스 잔여물을 용해하는 동시에 흡수합니다.
세척 효과를 높이기 위해 에어로졸 플럭스 제거제의 스트로 부착장치를 사용하는 방법
더 잘 분사하기 위한 스트로 부착장치를 사용하여 용제 잔여물을 제거합니다. 또한, 스트로는 정확하게 분사하는데 유용합니다. 따라서 사용자는 아래에 잘 조준할 수 있었습니다. 스트로 부착장치가 없으면 해당 부위 (예를 들어, 구성품 측)에 분사되긴 하지만 대부분의 물질이 쓸모 없어지게 되었습니다 (see Figure 1).
Figure 1: Visual comparison of an aerosol spray without (left) and with a straw attachment.
에어로졸 플럭스 제거제로 구성품 아래를 세척하는 방법
오염된 구성품의 모서리와 측면이 해결되면 가장 좋은 결과를 얻었습니다. 모서리에 직접 용제를 분사하면 플럭스 댐을 분해하는데 유용했습니다. 구성품 측면을 다룰 때 모서리를 먼저 세척하기 때문에 채널을 통해 용제가 더 많이 흐르게 되었습니다. 개방 채널이 더 많을수록 플럭스가 용제에 더 많이 노출될 수 있어서 구성품 아래에 플럭스가 포집되어 구성품 아래에서 유출됩니다.
진동 또는 고정 스프레이 사용 여부는 구성품 크기에 따라 달랐습니다. 소형 구성품의 경우 구성품 측면에 고정 스프레이는 충분하지 않았지만 더 큰 구성품의 경우 구성품 양측에 스프레이가 앞뒤로 진동할 때 기판이 더 깨끗해졌습니다. 이 진동 스프레이는 여러 각도에서 구성품 아래에서 용제가 위로 흐를 수 있었습니다.
Does the Angle of The Spray Affect Cleaning Effectiveness When Using an Aerosol Flux Remover?
이 시험에서 스트로 각도는 기판에 대해 30o, 45o 또는 60o이었는데 기판의 청결도에 영향을 주지 않았습니다. 일반 하향 또는 상향 각도는 충분했습니다. 스트로를 최대한 활용하기 위해 잔여물이 이동해야 하는 방향에 대해 생각해야 합니다. 구성품 아래에서 잔여물을 제거할 때 용제가 흘러야 하는 각도로 기판에 가깝게 분사합니다. 구성품 아래에서 잔여물을 전부 제거하면, 구성품에서 용제가 가장자리를 따라 나오게 되는 각도로 구성품에 분사합니다.
브러시, 스왑, 와이프와 같은 세척 공구를 올바르게 사용하는 방법
핸드헬드 브러시와 스왑은 처음보다 기판이 더 더러워 보이게 하고, 구성품 주변에 일부 플럭스가 젖어 있다가 마르면 흰 잔여물이 됩니다. 폴리우레탄 폼 스왑은 이 용도에 유용하지 않습니다. 폼 스왑은 강력한 용제로 적시면 물러지고 쉽게 찢어졌습니다. 또 다른 핸드헬드 공구 문제는 용제가 너무 빨리 증발되는 것이었습니다. 마지막으로 린스를 활용할 때 가장 결과가 좋았습니다 (see Figure 2). 핵심은 기판이 마르지 않게 하는 것입니다. 기판이 마르면 용제에 적었던 플럭스가 마르면서 흰 잔여물이 됩니다. IPA와 같이 천천히 증발하는 용제는 증발 문제를 피하지만 린스가 뒤따라야 합니다 (아래에 린스에 관한 더 상세한 내용 참조). 또한, 일부 용제는 문지르는 동안 구성품 아래에서 이동할 수 있지만 에어로졸 분사력 없이 구성품 아래에 있는 잔여물이 밖으로 밀려나갈 가능성이 희박합니다.
그림 2: 핸드헬드 브러시로 세척한 기판. 구성품을 적신 다음 브러시를 적시고 오염 부위를 문지릅니다. 첫 번째 그림의 기판은 마무리 린스를 거치지 않았습니다. 두 번째 그림의 기판은 린스로 마무리한 상태입니다 (참고: 모든 플럭스가 제거되지 않았음).
일부 솔벤트 세척제는 스프레이 헤드에 직접 부착되는 브러시와 함께 제공되며, 천천히 브러시를 통해 용제가 흐릅니다 (그림 3 참조). 이는 특히 유럽에 있는 디플럭서(defluxers)에서 일반적입니다. 브러시 부착장치는 일정하게 용제가 나오기 때문에 핸드헬드 공구보다 더 나은 결과가 나왔습니다. 그러나, 세척 시 에어로졸에서 관찰되는 동일한 수준의 청결도는 보이지 않았습니다. 브러시 부착장치는 문제가 되는 부위에 문지를 수 있지만 스트로 부착장치를 통한 에어로졸 분사력은 비슷한 결과를 보여주었습니다.
핸드헬드 공구와 같이 브러시 부착장치는 새 오염물이 유입될 가능성이 있습니다. 또한, 브러시 부착장치를 최대한 활용하기 위해 구성품 아래 세척과 마지막 린스에 별도의 에어로졸이 필요합니다. 에어로졸 분사력이 없는 핸드헬드 공구와 같이 일부 용제는 문지르는 동안 구성품 아래에서 이동할 수 있습니다. 그러나, 구성품 아래의 잔여물이 밀려나올 가능성이 희박합니다. 브러시 부착장치를 사용하려면 해당 부위가 젖어야 하고, 세척하는 내내 완전히 젖어 있어야 합니다. 이것은 완전히 제거되는 대신 기판에 잔여물이 다시 생길 수 있는 가능성이 높아지게 합니다. 마지막 린스는 기판에서 잔여물이 전부 제거되는데 매우 중요하였습니다 (그림 4 및 5를 참조합니다).
에어로졸이 연속으로 공급되는 세척용 분리형 브러시 기능이 있는 브러시 시스템이 있습니다. 브러시 부착장치와 비교하여 이 시스템의 세척 장점은 관찰되지 않았습니다. 브러시 시스템 또는 부착장치는 종종 용제 사용량을 줄이는데 사용되지만 잘 린스를 사용할 때 이러한 장점이 크게 감소합니다.
그림 3: 브러시 부착장치
그림 4: 브러시 부착장치로 세척한 기판 (별도의 에어로졸 사용하지 않았음). 사전 린스 또는 최종 린스 활용되지 않음. QFN B 및 QFP 주변에 각각 보이는 흰 잔여물.
그림 5: 브러시 부착장치로 세척한 기판 (사전 린스와 최종 린스에 별도의 에어로졸 사용됨). QFN B 및 QFP 주변에 각각 보이는 일부 흰 잔여물.
PCB 세척 시 최종 린스가 필요한 때
시험에서 최종 린스가 필요하다고 발견되었습니다. 이 단계에서 용제에 적신 플럭스 잔여물이 구성품 아래와 주변에서 제거되고 기판에서 완전히 유출되어 다시 생기지 않게 할 수 있습니다.
아무도 차이점을 볼 수 없는데 구성품 아래를 잘 세척하기 위해 노력과 경비를 들이는 이유가 무엇일까요? 결국 전자제품에 필요한 신뢰도 때문입니다. 플럭스로 조립되는 일회용 전자 장치의 경우, 전체 린스가 필요할 수 있습니다. 더 높은 신뢰성이 요구되면 이온 오염으로 인한 최종 장치 고장을 방지하기 위해 관리가 더 필요합니다. 시간과 노력을 들이는 것은 종종 금전적 소비가 따릅니다.
대부분의 인기있는 전자장치 세척제?
전제제품 조립 및 수리 과정에서 화학물질이 발견되지만 이소프로필 알코올보다 일반적으로 쓰이는 용제는 없습니다. 이 물질은 세척에 범용으로 쓰이고 플럭스의 주요 구성분으로 사용되지만 이소프로필 알코올이 얼마나 알려져 있을까요?
이소프로필 알코올 (CAS #67-63-0)은 IPA, isopropanol, 2-propanol로도 불리우며, 소독용 알코올이라고도 합니다. 다양한 극성 및 비극성 오염물을 용해시키며, 종종 경유, 지문, 절삭유, 플럭스 잔여물, 탄소 적층물, 이형물을 녹이고 제거하는데 쓰입니다. 또한 물에 쉽게 혼합되기 때문에 건조제로도 쓸 수 있습니다.
전자 인쇄 회로 기판(PCB) 조립의 경우, 최근에 납땜한 회로 기판 또는 PCB 수리 및 재작업에 플럭스 잔여물을 제거하는데 이소프로필 알코올이 사용되는 것을 볼 수 있습니다. 또한 IPA는 SMT 스텐실에서 접착제 또는 납땜 페이스트를 제거하는데도 사용됩니다. SMT 리플로우 오븐, 웨이브 납땜 핑거, 선택적 납땜 노즐, 팰릿, 자동 납땜 과정에서 플럭스가 생기는 부위에서 두꺼워지거나 연소된 플럭스를 제거하는데 이소프로필 알코올을 이용한 유지보수 세척은 일반적입니다.
대부분의 다른 플럭스 제거제는 특정 플럭스, 광범위하게 혼합된 플럭스, 특정 세척 과정에 사용할 수 있습니다. PCB 세척 작업을 개선하는 방법에 대해 더 자세한 내용에 대해 켐트로닉스에 문의하시기 바랍니다 ( [email protected] 또는 770-424-4888).